The rhythmic clickety-clack of train wheels passing over rail joints has long been an iconic sound of rail travel. However, modern railway engineering has been steadily working to eliminate this familiar sound by implementing long-welded rail (LWR) technology. This innovative approach to track construction has revolutionized railway infrastructure, offering improved safety, reduced maintenance costs, and enhanced passenger comfort.
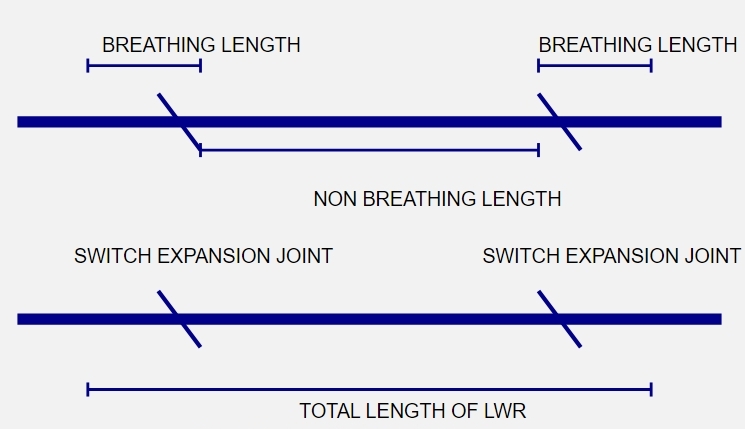
The Evolution of Rail Joints
Traditionally, railway tracks were constructed using individual rail sections connected by fish plates and bolts. While this method served the industry well for over a century, these joints represented the weakest link in the track structure. They required about 25% more maintenance effort than the rest of the track and created numerous operational challenges.
The problems associated with conventional rail joints include:
– Increased wear and tear on both rails and rolling stock
– Higher maintenance requirements
– Reduced passenger comfort due to impact forces
– Speed limitations
– Greater noise pollution
– Increased risk of track failure
Long-welded rail technology emerged as a solution to these challenges. By welding individual rail sections together into much longer continuous lengths, railways could eliminate most problematic joints. LWR represents a significant advancement in track technology, where rails are welded together to form continuous lengths extending up to an entire block section.
How LWR Works
The fundamental principle behind LWR involves what engineers call “locked-up stresses.” In a conventional track, rails expand and contract freely with temperature changes. However, in LWR, the central portion of the welded rail section remains stationary, while only the end portions (known as “breathing lengths”) experience movement due to temperature variations.
This behavior is achieved through:
1. Proper ballast resistance
2. Robust fastening systems
3. Adequate sleeper density
4. Careful temperature management during installation
The equation expresses the mathematical relationship governing thermal forces in LWR:
P = E × A × α × T
Where:
– P is the force in tonnes
– E is the modulus of elasticity of rail steel
– A is the cross-sectional area of the rail
– α is the coefficient of linear expansion
– T is the temperature variation
Technical Requirements for LWR Installation
The forces that arise because of temperature fluctuations of LWR installations require that the railway track be constructed to fulfill technical requirements. Those technical requirements of Indian standards,s for instance, mentioned below make sure the materials, construction, and parts can resist those forces.
Formation and Ballast
The success of LWR implementation heavily depends on proper track structure. Key requirements include:
1. Formation:
– Must be stable and trouble-free
– Should have a cross slope of 1 in 30
– Extra cess width for concrete sleeper track
2. Ballast:
– Minimum clean ballast cushion of 250mm below sleepers
– Shoulder width of 350mm for straight track
– Increased shoulder width of 500mm for curve outer sides
– Ballast should be heaped to 100mm height on shoulders
Sleeper Requirements
Different gauge sizes have specific sleeper requirements:
Broad Gauge (BG):
– Concrete sleepers with elastic fastening
– Treated hardwood sleepers with elastic fastening (speeds up to 160 km/h)
– Steel trough sleepers with elastic fastening (speeds up to 130 km/h)
Sleeper density varies from 1340 to 1660 sleepers per kilometer, depending on:
– Traffic density
– Operating speeds
– Route classification
Rail Specifications
LWR implementation requires specific rail types:
– 60 kg, 52 kg, or 90 R rails for broad gauge
– 90 R or 75 R rails for meter gauge
– New rails should preferably be free of fish bolt holes
Temperature Management requirements
Rail Neutral Temperature (RNT): LWR must be laid at an optimal neutral temperature to prevent rail buckling or pull-apart issues. Temperature records during installation are crucial.LWR must be installed considering the rail stress-free temperature (typically around 27°C for UK conditions).
Anchoring: The rail must be anchored properly using specific patterns to prevent longitudinal movement and provide stability
Courtesy of railroadpart.com
Temperature Management: Destressing is necessary using Rail heaters or expanders if the ambient temperature is below the ideal RNT. This ensures the rail length is adjusted to prevent stress.
Inspection Regime: Regular inspections, particularly after maintenance or temperature changes, are mandatory to monitor rail integrity.
Documentation and Recordkeeping: Comprehensive records are kept for temperature conditions, installation data, and adjustments made during and after post-installation.
Temperature considerations in maintenance vary by welded rail type:
SWR:
– Regular maintenance is done unless severe temperature changes occur.
LWR and CWR:
– Installation temperature carefully controlled
– Destressing operations critical
– Continuous monitoring required
Advantages of Long Welded Rail
The implementation of LWR offers numerous benefits:
1. Reduced Maintenance Costs
– Fewer joints to maintain
– Lower wear and tear on track components
– Reduced labor requirements
– Extended track component life
2. Improved Ride Quality
– Elimination of joint impacts
– Smoother rail surface
– Reduced noise levels
– Enhanced passenger comfort
3. Operational Benefits
– Higher permissible speeds
– Reduced energy consumption
– Lower rolling stock maintenance
– Improved track stability
4. Environmental Benefits
– Reduced noise pollution
– Lower material consumption
– Decreased energy usage
– Extended infrastructure life
Understanding Rail Welding Classifications
To understand the development of rail types in the railway industry, it’s important to know the different types of welded rail configurations used in modern railway systems:
Short Welded Rail (SWR)
Short welded rail consists of 3 to 5 rail lengths welded together. On Indian Railways, the standard has been set to 3-rail lengths (39 meters for broad gauge and 36 meters for meter gauge). SWR’s key characteristic is that it expands and contracts throughout its entire length in response to temperature changes, following normal expansion/contraction principles.
Long Welded Rail (LWR)
A long welded rail is defined as a welded rail length where the central portion does not undergo any longitudinal movement due to temperature variations.
In Indian railways, for a rail section to function as LWR, it typically needs to be:
– Greater than 250 meters on broad gauge
– Greater than 500 meters on meter gauge
– Maximum length typically limited to one block section under Indian conditions
The “breathing length” (the portion that moves with temperature changes) is typically about 100 meters at each end for broad gauge tracks under Indian conditions.
Continuous Welded Rail (CWR)
Continuous welded rail is essentially an LWR that extends through points and crossings in yards. It represents the next evolution in welded rail technology, allowing for even longer continuous sections and fewer expansion joints. Some modern railway systems have implemented CWR for several miles without any expansion joints.
Comparison of SWR, LWR, and CWR
The comparison table clearly illustrates the progression from SWR to LWR to CWR, showing how each advancement has brought improvements in track performance and maintenance requirements.
While SWR offers some advantages over traditional jointed tracks, LWR and CWR represent more sophisticated solutions that provide better long-term performance and reduced maintenance needs.
The choice between these systems often depends on various factors including:
– Track location and geometry
– Traffic density and speed requirements
– Maintenance capabilities
– Available budget
– Local climate conditions
Future Developments: Continuous Welded Rail
The evolution of welded rail technology continues with the development of Continuous Welded Rail (CWR). This advancement takes the concept of LWR further by:
– Extending beyond single block sections
– Passing through points and crossings
– Eliminating the need for expansion joints
– Further reducing maintenance requirements
The progression from SWR to LWR to CWR represents the evolution of rail technology:
– SWR: Initial step away from traditional jointed track
– LWR: Current standard for modern mainline railways
– CWR: Future of railway track with minimal joints and maximum efficiency
European railways, particularly in Germany and Britain, have successfully implemented CWR systems extending for several miles without expansion joints, even through station yards.
Long-welded rail technology represents a significant advancement in railway track engineering. While it requires careful planning, precise installation, and specialized maintenance procedures, the benefits far outweigh the challenges. The reduction in maintenance costs, improved ride quality, and enhanced operational capabilities make LWR an essential component of modern railway infrastructure.
As railway systems continue to evolve, the progression from jointed track to LWR and eventually to CWR demonstrates the industry’s commitment to innovation and improvement. The success of LWR implementation worldwide has proven its value in creating more efficient, comfortable, and sustainable railway networks.
The future of rail infrastructure lies in the continued refinement of welded rail technology, with ongoing research and development focused on:
– Enhanced installation techniques
– Improved monitoring systems
– Advanced maintenance methods
– Extended application possibilities
As we move forward, the classic sound of wheels clicking over rail joints may become a distant memory, replaced by the smooth, quiet operation of trains on welded rail – a testament to the advancing technology that keeps our railways moving forward.
Sources:
CWR track definition. When is the track not “jointed” anymore? | A railway track blog
Continuous Welded Rail Distribution & Unloading Machine | Herzog
Force diagram for CWR under temperature variations | Download Scientific Diagram
Your writing is not only informative but also incredibly inspiring. You have a knack for sparking curiosity and encouraging critical thinking. Thank you for being such a positive influence!
Your blog is a treasure trove of valuable insights and thought-provoking commentary. Your dedication to your craft is evident in every word you write. Keep up the fantastic work!
Yeah bookmaking this wasn’t a high risk conclusion outstanding post! .